MOTION CONTROL FEATURES
Ability to operate in either machine axes or component axes.
System Manager / Programmer / Operator access levels with only the appropriate menus and options available in each case.
Full system status information is always readily available.
On-line and context sensitive help facility.
Comprehensive manual and automatic learn procedures.
Ability to mathematically add further internal surface lines providing different scan start positions, or for leading on to a more detailed automatic surface learn.
Full 3D image rotation enabling the part surface to be viewed from any direction.
Mathematical surface extension to allow the over scanning of edge regions.
Extraction of sub-surface regions to generate further scan plans.
Full control of all possible scan parameters and machine variables.
Fast network communications with the data acquisition system for scan control synchronization during scan start and scan error recovery.
Provision of data acquisition trigger pulses synchronized with the complex contoured surface being tracked during scanning motion even during acceleration and deceleration phases to ensure the correct spacing of ultrasonic acquisition points throughout the whole part surface.
Network communications with the data acquisition system at the start and end of each scan line to verify the number of trigger pulses and the integrity of the ultrasonic data being collected.
Ability to stop a scan then return the next day and continue from where you left off with both systems being automatically setup as before through the motion control scan plan and the acquisition workspace.
Provision of 3D surface data to the data acquisition system to enable 3D mapping of ultrasonic data to the actual part shape to remove any potential for image distortion.
Area re-scan capability initiated by selecting a region from an acquisition image leading to only that region being re-scanned with the ultrasonic data being over-written facilitating the removal of air bubble or other spurious effects.
Return to defect capability enabling the machine to be positioned back directly over a defect for further analysis.
After return to defect an option to switch joystick control into a different mode so that the Z-axis joystick will move the machine towards or away from the part along the surface normal. At the same time the X/Y axes joystick will move the machine in a plane parallel to the surface at the return to defect location.
Whole range of calibration options to enable determination of machine accuracies, machine Squareness, and manipulator qualification.
Comprehensive transducer qualification options allowing determination of all transducer variables including length and squint angle.
Cycle axes options to facilitate assessment of machine performance.
Hand-box Keypad and LCD-Display communication to enable remote control capability under all appropriate circumstances through display menus and keypad function buttons.
Hand-box high/slow speed button for fine adjustments when necessary.
X/Y joystick orientation control so that no matter which way the operator is facing the X/Y axes will always move intuitively according to the joystick direction.
|
Winspect from
- Bringing the convenience of Windows to ultrasonic testing... |
Simple on-screen control |
Winspect introduces the proven framework of Microsoft Windows to nondestructive testing,
enabling you to perform ultrasonic tests and manage data with unparalleled ease. Winspect
offers many time-saving features including toolbar commands, pull-down menus, user-defined colors,
multiple displays and context-sensitive Help. With simple on-screen commands, set gates, select scan
parameters, define output format and save the setup and results to disk. |
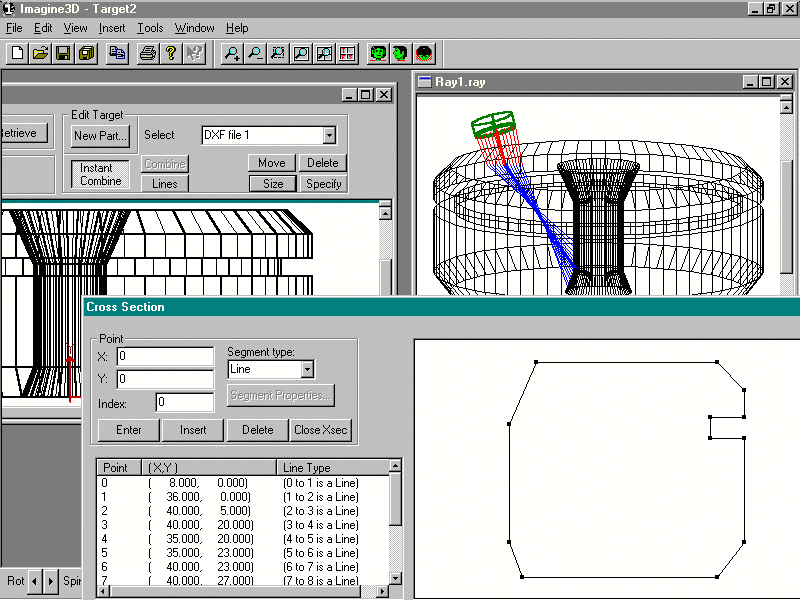 |
Multi-tasking capabilities |
Winspect takes you a generation beyond dedicated, single purpose data acquisition computer systems.
Winspect will control your scanning rig, collect the data and simultaneously control auxiliary instrumentation.
Data and images can be transferred directly to other software packages for analysis and report preparation.
This exceptional flexibility provides significant time and cost savings. |
Designed for value |
Integrate Winspect with your existing hardware. Software support is available for a broad range of acquisition
and control hardware and can be provided for new components. Testing capabilities are dramatically upgraded and
unnecessary capital expenditures avoided by adding this sophisticated software to your existing system. Winspect
delivers outstanding value at a competitive price. |
Winspect is an advanced data acquisition software package built on the unique convenience and flexibility of the Windows platform.
|
In ultrasonic applications, Winspect provides data recording, motion control, pulser receiver control, data display and
signal processing enhancements. Winspect records time of flight, amplitude and waveform data from within up to four gates
per channel. Data can be displayed in conventional A, B, and C-scan formats and in three dimensional views.
Signal processing routines, such as data averaging and digital filtering, which improve signal quality, are included in
Winspect. Fast Fourier transform processing is also provided for transducer characterization. |
Save time with Winspect. With a simple click of the mouse, the motion control system will re-position to any point of
interest on a C-scan. Examine details down to the pixel level by using the continuous zoom feature. Test results and instrument
settings can be saved to disk for future reference, allowing side by side comparison of current and archived data in multiple windows.
|